Digital transformation and corporate culture
2023-09-06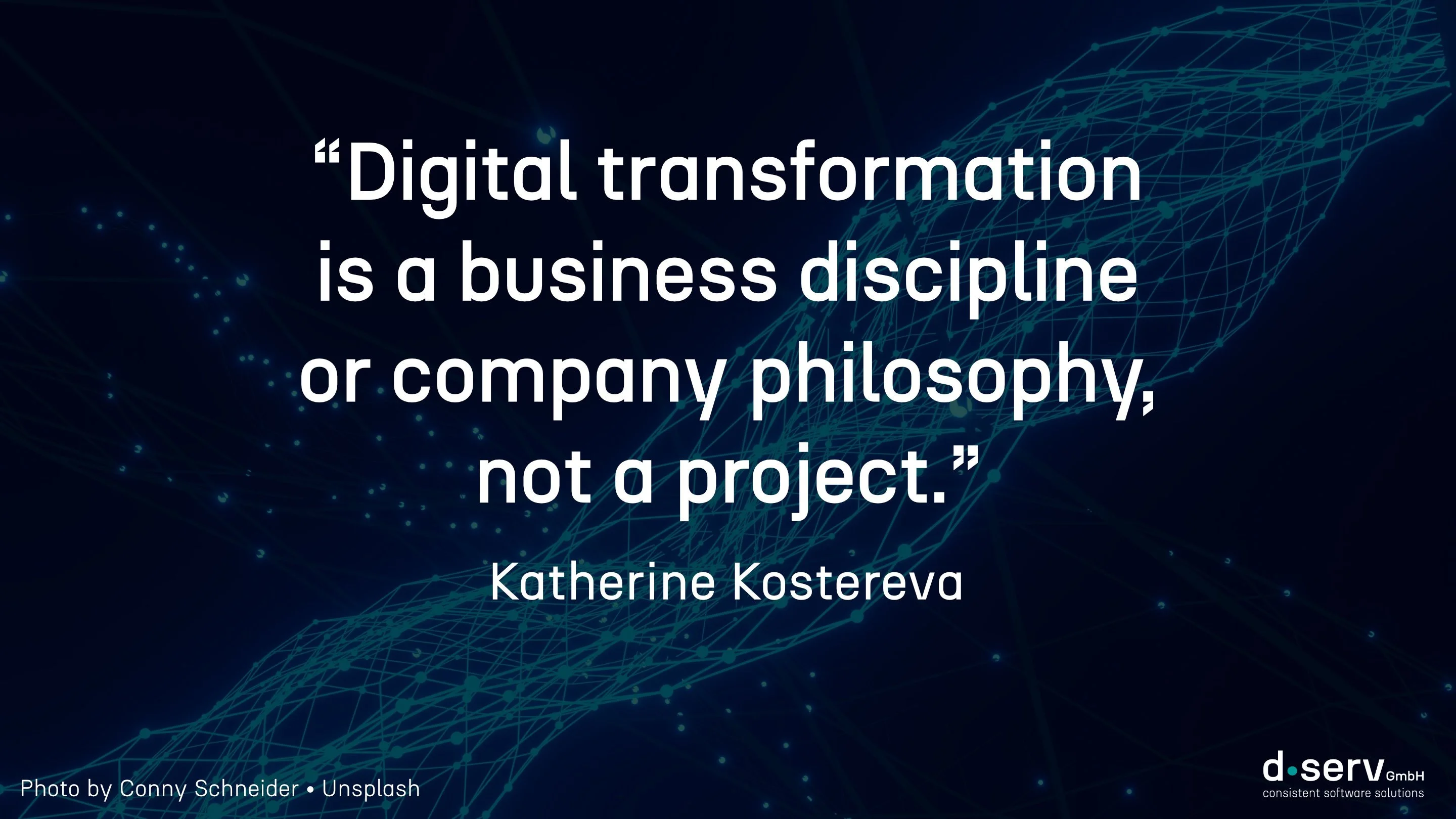
Introduction
The frequently cited digital transformation and the agile processes described as necessary in this context primarily require teams that support this approach and are encouraged to do so by a corresponding corporate culture. Every transformation always starts in the "heads" and if they do not want to "go along", all process optimisations cannot be implemented or are not feasible in the long term. Mutual trust and transparency plus jointly defined goals and a mutual interest in achieving these goals are the cornerstones of improved processes and successful projects. Mutual means both between client and contractor, as well as within the respective companies, between all employees involved in the project. As part of the pilot project "Agile teams - success factors for cross-company and cross-industry cooperation in the digital transformation" funded by the Baden-Württemberg Ministry of Economic Affairs in 2021 with the project partners Ferdinand-Steinbeis-Institut, Steinbeis 2i GmbH and bwcon GmbH, the agile team at d-serv GmbH gave an insight into its corporate culture and successful collaboration with Stuttgart-based Koenig & Bauer MetalPrint GmbH.
Task and challenges for the client
The internationally active Koenig & Bauer MetalPrint GmbH from Stuttgart assembles and maintains machine lines worldwide as a machine and plant manufacturer. These include printing machines for metal printing, such as those used for beverage cans and tins. The Koenig & Bauer MetalPrint GmbH service team has to set up these complex machine lines initially, maintain them continuously and expand them as required. The challenges include
- Delivering and setting up at locations that have an unstable or reduced infrastructure in terms of mobile communications or internet connection.
- The service team must document any process disruptions according to standardised specifications and uniform processes and report them to the head office both completely and promptly.
- The time span from recognising, recording and transmitting the process disruption to its rectification, especially if this cannot be done by the service team alone on site but only with the help of the control centre and specific feedback, must be as short as possible in line with the requirements of industrial production.
To overcome these challenges, the Koenig & Bauer MetalPrint GmbH service team needs a solution that is capable of collecting all data and relevant information in advance, even without a permanently available internet connection, and transmitting it immediately to the head office or all relevant departments and specialists if the internet connection is intact and working.
Procedure and solution of the contractor
As part of a joint workshop between Koenig & Bauer MetalPrint GmbH and d-serv GmbH, the requirements for the machinery and plant engineering division were defined, the critical process steps identified and agreed with the relevant user groups. After analysing the requirements, the decision was made in favour of the IQM platform. The IQM platform, a web-based database application, has already been used successfully for years in the construction industry and in plant engineering to record construction defects on major construction sites. Based on the specific requirements of Koenig & Bauer MetalPrint GmbH for the machinery and plant engineering sector, the IQM platform was customised with the support of d-serv GmbH. This meant that the pilot phase could begin early and a platform with the desired basic functionalities and the planned extensions could be provided promptly, which was then used for both ongoing and new projects with different user groups at different locations. During this pilot phase, the focus for the project managers was on recording and analysing user experiences and providing the data in the usual reporting format. The IQM platform, accessible for desktop use using modern browsers, and the associated native applications for use on mobile devices based on iOS or Android, are designed in such a way that simple, structured and guided input is guaranteed even without an existing internet connection and the data entered can be securely transmitted or synchronised at a later date. The Koenig & Bauer MetalPrint GmbH service teams were able to use the IQM platform/applications immediately without any further hurdles or training costs, with the acceptance achieved leading to an increase in user numbers at the same time.
Additional information
- Website of the Koenig & Bauer MetalPrint GmbH from Stuttgart: https://metalprint.koenig-bauer.com
- The published article from the Steinbeis Magazine "Transfer", Issue 02/21, p. 78-81 as PDF for download.
- The documentation of the results of the pilot project and the resulting catalogue of measures on the website of the Ferdinand Steinbeis Institute as PDF for download.